| Calling Van HelsingA hands-on investigation into the myth and reality of the original anti-werewolf weapon: silver bullets. |
| |
| |
Like darning socks, making bullets is a dying art. Used to be just about everyone with a need for ammo poured their own, using iron or even wooden molds. These days only a few diehard hobbyists still do it, and they use aluminum molds. But even fewer people still make silver bullets.
Actually, not many people ever made silver bullets. It's a difficult process, and their efficacy against werewolves has never been scientifically proven. I suppose their renown came from the perception that silver was a distinguished metal, often spoken of in connection with its higher-class cousin, gold. But today silver is far more common, and it tarnishes over time, primarily because of sulfur pollution from power plants. (By and large, it didn't tarnish before the Industrial Age.)
I couldn't find any references describing real historical silver-bullet-crafting techniques. At 1,764°F, molten silver would ruin traditional and modern bullet molds. They could have been fashioned using jewelers' methods, but that would require a new plaster mold for every bullet. Frankly, I think people spent a lot more time talking about silver bullets than they did turning them out. I don't like legends that are all talk, so I decided to see what it takes to produce a real silver bullet: not plated, not sterling-pure silver.
To create the mold, I first had to construct a bit. I used a lathe to turn a steel rod into a bulletlike shape, then used a milling machine to cut away a quarter-circle wedge of the rod, leaving a sharp cutting edge. Basically I had built a router bit shaped like a bullet. (I've fabricated bits like this freehand with a file; which works fine, it just takes longer. Much longer.) After using the bit to machine the graphite bullet mold, I used an electrically heated graphite crucible to pour in 0.999 fine liquid silver at about 2,000°F, which is 230°F above its melting point. The mold must be preheated with a blowtorch to keep the silver from solidifying before it fills the whole cavity. One of the benefits of using graphite is that it keeps the silver from oxidizing, so bullets come out bright and shiny.
Would a silver bullet really fire? Probably. (Though, not being an experienced gunsmith, I would never be foolish enough to try my bullets in a real gun.) Bullets need to be fairly soft so that they can take on the shape of spiral grooves in the gun's barrel, and pure silver is moderately soft. It's also similar in density to lead, so it should have similar aerodynamics and muzzle velocity. I'd guess silver would make a very nice nontoxic substitute for lead in bullets. Too bad about the cost: These one-ounce, large-caliber rifle bullets use about $7 worth of silver per shot-best reserved for only the most severe werewolf infestations.
Scan of printed version:
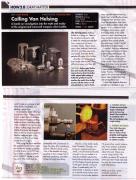 |
| |
| |
|
| |
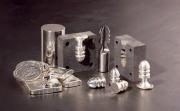

A lathe forms the bullet shape, including its sprue and pouring funnel. The rounded tip is smoothed with a file and sandpaper after rough cutting.
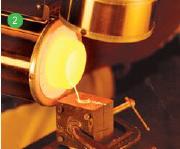
Four steel index pins and a clamp hold the two halves of the graphite mold together as silver is poured from an electric crucible.
Photo Credits: Mike Walker Mike Walker Mike Walker
|
|